Product classification

Mobile: +8618624918289
E-mail: 290004946@qq.com
Address: Xingyang Gaoshan Town Valve Industrial Park
Full-bore filter 2024
The GL41H-16Q full-bore filter is a special filtering device designed to allow fluid to flow freely through the full-bore passage, thereby reducing fluid resistance and pressure drop, and improving system efficiency.
Full-bore filter 2024
Full-bore filter
Full-bore filter, a cutting-edge technology in the field of filtration, has revolutionized the way we remove impurities from liquids. Unlike traditional filters, full-bore filters are designed to minimize pressure drop and maximize flow rates, making them highly efficient and cost-effective. In this article, we will explore the benefits and applications of full-bore filters, as well as their impact on various industries.
At the core of the full-bore filter technology is its design, which allows for maximum flow rates without compromising filtration efficiency. Traditional filters often suffer from pressure drops that decrease flow rates and increase energy consumption. Full-bore filters, on the other hand, are designed to maintain a consistent flow rate while removing impurities from liquids, resulting in significant cost savings for businesses.
One of the key benefits of full-bore filters is their versatility. They can be used in a wide range of industries, including oil and gas, chemical processing, food and beverage, and pharmaceuticals. Whether filtering water, oil, chemicals, or other liquids, full-bore filters provide superior filtration performance and can be customized to meet specific industry requirements.
In the oil and gas industry, full-bore filters play a crucial role in ensuring the quality and purity of petroleum products. By removing impurities such as dirt, sand, and debris from crude oil and natural gas, full-bore filters help prevent equipment damage and improve the efficiency of refining processes. Additionally, full-bore filters are essential for maintaining the integrity of pipelines and storage tanks, reducing the risk of contamination and costly maintenance.
In the chemical processing industry, full-bore filters are used to remove contaminants from chemicals and solvents, ensuring product quality and consistency. By maintaining a high flow rate and efficient filtration performance, full-bore filters help companies meet regulatory requirements and reduce waste disposal costs. Additionally, full-bore filters can be easily integrated into existing filtration systems, making them a cost-effective solution for businesses looking to improve their filtration processes.
In the food and beverage industry, full-bore filters are essential for maintaining the purity of liquids such as water, juice, and dairy products. By removing particles, bacteria, and other impurities from these liquids, full-bore filters help ensure product safety and quality. Additionally, full-bore filters can help extend the shelf life of perishable products by preventing contamination and spoilage.
In the pharmaceutical industry, full-bore filters are used to remove contaminants from drug formulations and sterile solutions. By maintaining a high level of filtration efficiency, full-bore filters help pharmaceutical companies meet strict regulatory standards and ensure the safety and efficacy of their products. Additionally, full-bore filters can be customized to meet the specific requirements of different pharmaceutical applications, making them a versatile and reliable filtration solution.
In conclusion, full-bore filters are a game-changer in the field of filtration, offering unparalleled efficiency, versatility, and performance. Whether used in the oil and gas, chemical processing, food and beverage, or pharmaceutical industries, full-bore filters provide a cost-effective solution for improving filtration processes and ensuring product quality. With their design and superior performance, full-bore filters are set to revolutionize the way we remove impurities from liquids in various industries.
Plant
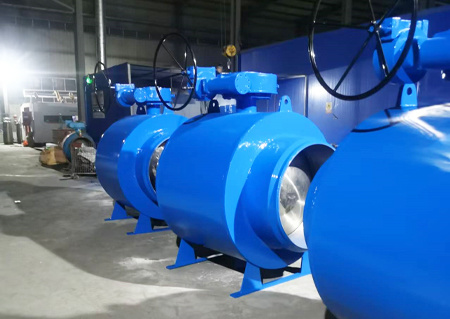
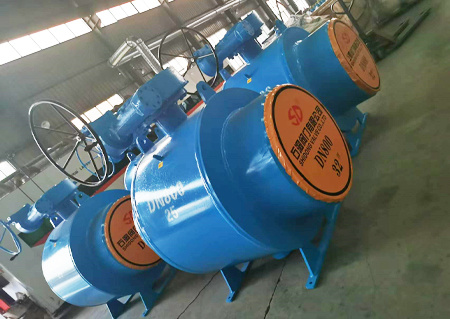
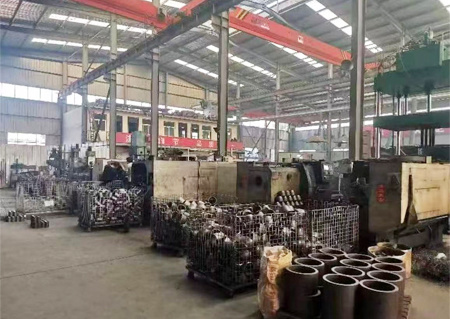
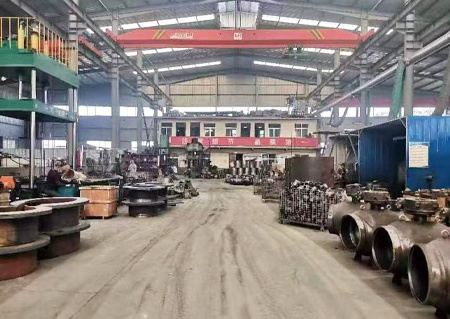
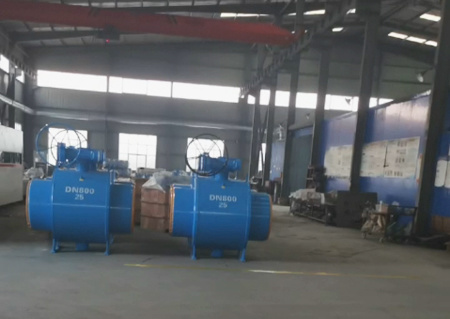
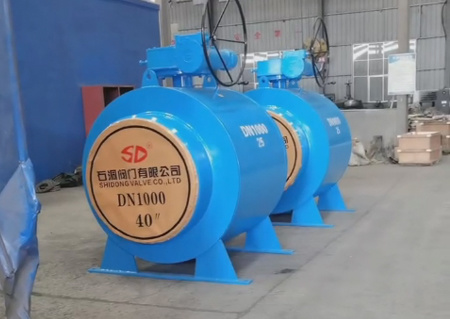
Application areas

oil and gas

Chemical industry

Food and beverage

Steam industry

Shipbuilding and Mining

Other industries
Honor

FAQ
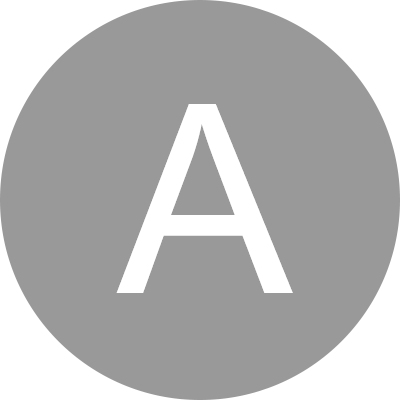
1. Before installation, check whether the specifications, pressure, temperature, and corrosion resistance of the butterfly valve meet the usage requirements. Inspect all parts for damage or looseness.
2. This butterfly valve can be installed on pipes at any angle, preferably in a closed position; when welding the pipe flange, cover the valve sealing surface with a plate to prevent particles and debris from damaging the sealing surface. After welding, remove the valve, clean the sealing surface and the inner cavity of the pipe, and then install and secure the valve.
3. During installation, pay attention to the pressure direction when the valve is in the closed state.
4. Before installation, thoroughly clean the sealing surfaces (both ends, butterfly plate sealing surface, and valve seat sealing surface) to remove dust and dirt.
5. Before installation, perform a trial operation of the butterfly valve; it should open and close smoothly, and the open/close position should match the pointer position. Manual operation: clockwise to close, counterclockwise to open; do not apply additional force once the pointer is in position.
7. When conducting pressure tests on the valve, do not use a single flange for installation and pressure testing; double flanges must be used. When tightening bolts, do so in a symmetrical and alternating manner; do not tighten them sequentially. 9. The limit bolts have been adjusted before leaving the factory and should not be easily adjusted. If the drive device is electric or pneumatic, please read the accompanying drive device manual.
10. If the valve opens and closes abnormally, investigate the cause for repair and elimination; do not use force to operate the valve, as this may cause damage. 11. If the valve malfunction cannot be resolved, please notify our company for product installation, usage, and after-sales service.
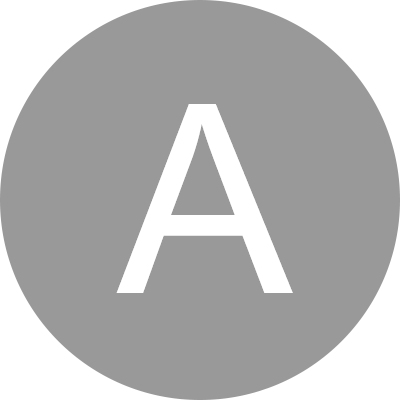
If there are no other special requirements for the valve, it can be ordered according to the valve's number. This requires the user to understand the valve number description when ordering the product. Although this may be difficult for the user, selecting the appropriate number based on the parameters of the product they need can ensure that the provided valve fully meets the user's requirements.
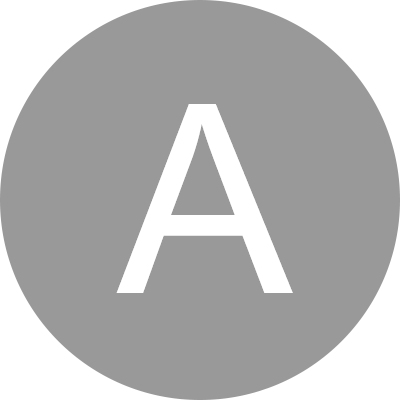
1. When storing, the valve passage at both ends must be blocked with cover plates. It should be stored indoors in a dry and ventilated environment, and should be regularly checked and cleaned of dirt. Anti-rust oil should be applied to exposed machined surfaces to prevent rust.
2. Valves must be stored in a dry room and should not be placed outside to avoid damage.
3. Before transportation, valves must be tested and debugged according to the requirements of the contract or standard requirements to prevent user misoperation. For pneumatic or electric ball valves, the power source requirements for the corresponding devices must be listed according to the instructions of the pneumatic or electric device. If the user needs testing and inspection, it must be conducted according to standard requirements to prevent the product from failing to meet its performance due to incorrect testing methods. After pressure testing, any accumulated water inside the valve must be cleaned out before storage.
4. When installing the valve, the cover plates at both ends of the valve must be removed. For valves connected by welding, protective measures must be taken during the welding installation process to prevent adverse effects on the valve due to high temperatures. 5. For valves with a specific installation direction, directional arrows must be marked on the valve body to prevent incorrect installation.
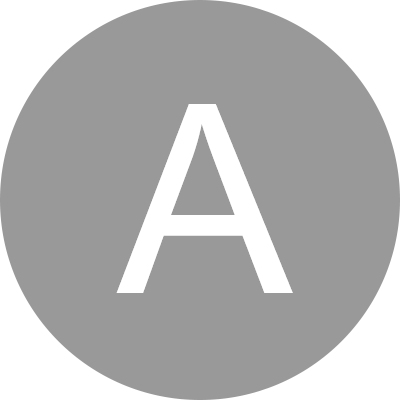
1. Manual valve: When the handle is in a parallel position to the pipeline, the valve is in the open position; when it is at 90 degrees, the valve is in the closed position. Turning the handle clockwise closes the valve, while turning it counterclockwise opens the valve.
2. Worm gear driven valve: Identify using the indicator device installed on the upper part of the valve; turning the handle clockwise closes the valve, while turning it counterclockwise opens the valve. 3. Valves operated by pneumatic, electric, gas-liquid linkage, or hydraulic linkage: Operate according to the relevant actuator manual.
Key words:
Full-bore filter 2024
Free Quote
Note: If you have any suggestions, please leave a message or send an email to us, and we will reply to you within 1 working day after receiving the message email.
Related Products